Производство шамотных огнеупорных материалов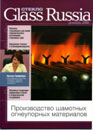 В ОАО «Эй Джи Си «Борский стекольный завод» завершены пуско-наладочные работы и начато производство шамотных огнеупорных блоков для футеровки флоат-ванн и стекловаренных печей на заводах по производству листового стекла, входящих в крупнейшую японскую корпорацию Асахи Гласе Компании (AGC). В одном из интер¬вью генеральный директор Борского стекольного завода Валерий Тарбеев назвал этот проект знаковым для предприятия.
Одним из основных технологических агрегатов в произ¬водстве листового полированного стекла является флоат-ванна, в которой на поверхности расплава олова осуще¬ствляется формование ленты стекла.
Качество получаемого флоат-стекла во многом оп¬ределяется качеством огнеупорных блоков, применяемых для футеровки дна флоат-ванны. С самого нача¬ла работ по методу флоат-процесса эти блоки изготав¬ливались на шамотной основе и, несмотря на появле¬ние новых огнеупорных материалов из алюмината кальция — SUPRALСА [1], разработанных компанией
RHI Refractories, шамотный донный брус является в настоящее время одним из наиболее востребованных изделий шамотного состава в стекольной промышлен¬ности [2].
В период 30 — 90х годов прошлого века все крупные стекольные заводы в СССР имели свои керамические участки для изготовления шамотных изделий: «лодочек» Фурко, мостов подмашинных камер и различного припаса для машин BBC. С переходом на изготовление флоат-стекла надобность в этой продукции отпала, и часть производств подобных изделий прекратило свое существование либо перепрофилировалось на производство других шамотных огнеупоров. Цех по производству шамотных огнеупоров на Борском стекольном заводе существовал с самого ос¬нования завода и в последнее время производил шамотный брус для футеровки дна флоат-ванн и донный брус для стекловаренных печей. Учитывая традиционно высокое качество шамотного донного бруса, производимого на Борском стекольном заводе, руководство компании AGC (Япония) приняло решение и в 2006г. открыло финансирование проекта строитель¬ства нового производства шамотных огнеупорных блоков для стекольных заводов, входящих в корпорацию. Проект дозировочно-смесительного отделения, изготовление и комплексную поставку технологического оборудования, его шеф-монтаж, а также пуско-наладочные работы на линиях обработки сырьевых материалов и приготовления шихты нового производ-ства шамотных огнеупоров выполнило ЗАО «Стромизмеритель», г.Нижний Новгород. Технологическая схема отделения приготовления шихты (рис 1.) в этом производстве работает следующим образом. Высушенная на участке предваритель¬ной обработки глина с помощью фронтального ков¬шового погрузчика 1 подается в приемный бункер скипового подъемника 2, который после перемещения его в крайнее верхнее положение, разгружает ма¬териал в промежуточный бункер 3 качающегося питателя 4. Питатель 4 с заданной интенсивностью работы, определяемой производительностью последую¬щих технологических механизмов, подает материал в щековую дробилку 5, из которой куски глины размером не более 20...40 мм транспортируются с помощью ленточного конвейера 6 в дезинтегратор 7 для после¬дующего измельчения до фракции 0,5 —0,7мм. Измельченная глина поднимается ковшовым ленточным элеватором 8 и через течку, оборудованную стержневым магнитным сепаратором 9 типа ACMK 400x400, направляется в сито барабанное полигональ¬ное 10 и далее после просева — в надвесовой расходный бункер 11 дозировочно-смесительной линии. Отсев более крупной фракции глины непрерывно воз¬вращается в дезинтегратор на повторное измельчение. Другой основной компонент шихты — огнеупорный шамот в виде так называемых «валюшек» (кусков глины диаметром 250 мм, полученных методом экструзии и обожженных при температуре 1320 °С в печи периодического действия) после обжига загружается в контейнер 12 и с помощью загрузчика 13 устанавливается на промежуточную площадку загрузки щековой дробилки 14, в которую материал подается вручную. Дробленый шамот конвейером ленточным 15 и элеватором 16 транспортируется в промежуточный бункер 17, уровень заполнения которого контролиру¬ется системой управления. Наличие подобного бунке¬ра в сочетании с вибрационным питателем 18 позволяет осуществлять плавную регулировку загрузки ме¬лющих бегунов 19 в независимости от интенсивности ручной подачи «валюшек» в щековую дробилку. 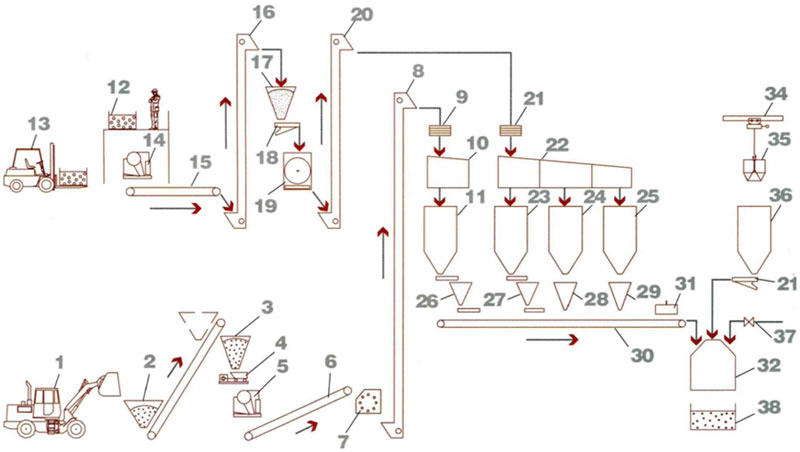
Первоначально для повышения производительно¬сти процесса помола вместо снятых с производства мелющих бегунов 19 в линии обработки и дробления шамота была установлена шаровая мельница, широко применяемая на других российских предприятиях по производству огнеупоров. Эксплуатация данного тех¬нологического агрегата при помоле шамота выявила следующие существенные недостатки. Таблица 1 НАИМЕНОВАНИЕ ДОЗИРУЕМОГО МАТЕРИАЛА | РАСХОД МАТЕРИАЛА НА ОДИН ЗАМЕС | ТИП ДОЗИРОВОЧНОГО КОМПЛЕКСА | Глина | 19-22 | КДУ-Ш-180-125-850-145Ш. НПД=180кг, V=145л | Шамот, Фракция до «100» до 0,7мм: | 78-81* | КДУ-Ш-180-125-850-145Ш, НПД=180кг, V=145л | Шамот, Фракция «49» от 0,7 до 1,2мм: | КДУ-Г-40-100-170-42С, НПД=40кг. V=42л | Шамот, Фракция «16» от 1,2 до 2,0мм | КДУ-Г-80-100-170-80С, НПД=80кг, V=80л | Вода | 6-8 | КДЖР-25-1 |
• суммарный расход фракций шамота «16», «49». «100» Таблица 2 НАИМЕНОВАНИЕ ПОКАЗАТЕЛЯ | ЗНАЧЕНИЕ ПОКАЗАТЕЛЯ | Длина бруса, мм Ширина бруса, мм | 454...990 608...642 | Высота бруса, мм | 254...338 | Массовая доля оксида алюминия (А1203) | | на прокаленное вещество, %, не менее Кажущаяся плотность, г/см3, не менее Пористость открытая, %, не более | 34 21 19 | Предел прочности при сжатии, мПа
Газопроницаемость по отношению к воздух, мкм2 (нПм) | 30...50
У.
0,05...0,2 (0,5...2) |
Полученная после измельчения исходного материала масса имела нестабильный гранулометрический со¬став из-за интенсивного истирания мелющих тел и большое содержание аппаратного железа во фракции шамота 0,7мм. Если требуемое пропорциональное соотношение между различными фракциями молотого шамота удалось получить с помощью подбора веса за¬гружаемых в мельницу шаров и пропорции шаров с от¬носительно большим и малым диаметром, то устранить аппаратное железо, которое в процессе помола созда¬вало трудноразделимые конгломераты с легкими час¬тицами шамота, не удавалось ни с помощью стержне¬вого, ни с помощью подвесного магнитных сепарато¬ров установленных в линии. Кроме того, во время сепа¬рации больше половины мелкой фракции шамота вме¬сте с железосодержащими частицами сбрасывалось в отсев во время регенерации магнитного сепаратора.
Дополнительные исследования по магнитной сепа¬рации и возможности выделения металломагнитных включений из шамота, проведенные специалистами фирм ЭРГА (г.Калуга) и ПРОДЭКОЛОГИЯ (Украина) с помощью более мощных магнитных сепараторов различной конструкции не позволили снизить исходное содержание железа с 0,256% до требуемой кон¬центрации 0,025%.
Предполагаемая замена металлических шаров на уралитовые мелющие тела, используемые в производ¬стве санитарно-технической керамики, была отклоне¬на из-за возможного натира глинозема и вследствие этого последующего повышения температуры обжига сформованных из полученной шихты огнеупорных блоков. А выполненная замена мелющих тел на более износостойкие шары, изготовленные из стали, иду¬щей на производство шарикоподшипников, позволи¬ла лишь в два раза снизить содержание аппаратного железа и не решила проблему полностью.
Поэтому по результатам нескольких месяцев не¬удовлетворительной эксплуатации шаровой мельни¬цы специалистами ОАО «AGC «Борский стекольный завод» и ЗАО «Стромизмеритель» было принято ре¬шение о замене шаровой мельницы на бегуны, которые работали в течение многих лет на старом керами¬ческом участке Борского стекольного завода.
После капитального ремонта и установки бегунов в технологическую линию приготовления шихты про¬блема с повышенным содержанием аппаратного же¬леза и его сепарацией была решена без использова¬ния дополнительных валковых и барабанных магнит¬ных сепараторов.
После измельчения в бегунах 19 шамот поднимается ковшовым ленточным элеватором 20 и через течку, оснащенную стержневым магнитным сепаратором 21, загружается в сито-бурат 22, в котором осуществляет¬ся разделение шамота по трем рабочим фракциям:
• фракция «100» до 0,7мм;
• фракция «49» от 0,7 до 1,2мм;
• фракция «16» от 1,2 до 2,0мм.
•
Полученные фракции шамота распределяются в соот¬ветствующие надвесовые расходные бункера 23, 24, 25. В случае переполнения бункеров 24 и 25 со сред¬ней и крупной фракциями во время работы линии по¬мола шамота предусматривается возврат материала в бегуны на дополнительное измельчение.
Из расходных бункеров 11, 23, 24, 25 глина и шамот трех фракций поступают в соответствующие дозато¬ры 26, 27 с винтовыми питателями загрузки и разгруз¬ки и дозаторы 28, 29 с гравитационными питателями. Расход материалов на один замес (меняется в зависи-мости от вида изделий) и тип весодозирующих комплексов представлен в табл. 1.
Из весовых дозаторов отдозированные материалы разгружаются на сборочный конвейер 30 закрытого исполнения и при транспортировании в смеситель 32 шихты дополнительно подвергаются магнитной сепа¬рации с помощью подвесного железоотделителя.
Дополнительно в смеситель 32 поступает вода для увлажнения шихты, расход которой измеряется сис¬темой 33, и отходы шихты, получаемые при формова¬нии шамотных изделий. Оборудование для подачи от¬ходов шихты в смеситель включает в себя электротельфер 34, кюбель 35, расходный бункер 36 и вибрационный питатель 37, работающий по времени в ре¬жиме объемного дозирования. Готовая шихта (время цикла дозирования и пере¬мешивания составляет 6,2 минуты) разгружается в кюбель 38 и с помощью погрузчика транспортируется на участок формования, где она засыпается в разбор¬ные металлические формы и подвергается ручному прессованию или трамбованию [3]. Технология формования изделий имеет свои осо¬бенности: засыпка шихты ведется слоями, а трамбование осуществляется с определенным давлением и тра¬екторией, при которой более тщательно трамбуются пристенные и угловые участки шихты в форме, что существенно снижает расслаивание шамотного бруса при эксплуатации. Отформованное изделие — «сырец» подвергается естественной сушке, которая про¬изводится в течение длительного времени при опре¬деленной температуре (максимальная температура 60 °С). Далее подсушенное изделие — «сырец» подверга¬ется обжигу в печи периодического действия с посте¬пенным повышением температуры до 1400— 1435 °С. Процесс обжига длится до 20 суток. После обжига и шлифовки, обеспечивающей тре¬буемую геометрию шамотного бруса, готовая продук¬ция поступает на склад.
Технические характеристики производимых изде¬лий представлены в табл.2. Все параметры соответствуют требованиям ГОСТ 7151-74, а высокое качество шамотного бруса, производимого в ОАО «Эй Джи Си «Борский стекольный завод» также подтверждается исследованиями в лабо¬раториях компаний «Главербель» (Бельгия) и «CERAM» (Англия), где данная продукция была при¬знана одной из лучших в мире. Для создания нормируемых условий работы и сокра¬щения пылевидных выбросов молотой глины и шамота предусматривается герметизация технологического оборудования и устройство систем аспирации, в кото¬рых воздух проходит очистку в рукавных фильтрах про¬изводства концерна «WAMGROUP» (Италия). Очищен¬ный в фильтрах воздух с остаточной запыленностью не более 2 мг/мЗ возвращается в помещение цеха. Включение и выключение систем аспирации сбло¬кировано с работой технологического оборудования, управляемого в автоматическом режиме с помощью микропроцессорной системы управления, построен¬ной на базе контроллера ICP серии 1-8000 и персо¬нального компьютера. Годовая производительность данного производства составляет 500 тонн и может быть увеличена до 650 тонн шамотных огнеупорных блоков, используемых для футеровки флоат-ванн и стекловаренных печей, на предприятиях по выпуску листового стекла в России, Франции, Японии, Индии, США, Китае, Чехии и других странах. В.В. Ефременков, К.Ю. Субботин, ЗАО «Стромизмеритель»,
Д.С. Альтов, Г.С. Нагибин, ОАО «Эй джи си - борский стекольный завод» Литература 1. Шмаленбах Б., Вайхерт Т., Сантановски К., Кучерявый М.Н. «Разработка огнеупоров для кладки дна ванны расплава в печах флоат-стекла» Glass Russia. Стекло, 2008, №6, с.54-64;
2. Россихина Г.С. «Огнеупоры для стекольной промышленности в России». Glass Russia. Стекло, 2007 №5, с.20-23;
3. Тарбеев В.В., Лукашин С.А., Шепелев Д.Н. «Строительство и ремонт стекловаренных печей» Нижний Новгород, «Нижполиграф», 2005, с.20-23. |