Могут ли асфальтосмесители типа ДС-158 быть конкурентоспособными на рынке дорожных услуг?27.03.2014
Технологическое оборудование для приготовления асфальтобетонных смесей на дорожном рынке в России более чем на 80% представлено асфальтосмесителями Кременчугского завода дорожных машин типа ДС-158. Отсутствие достаточных средств на техническое перевооружение не позволяет дорожным организациям произвести быструю замену технологического оборудования на более производительное и современное, полностью отвечающее высоким требованиям к качеству асфальтобетонной смеси и экологичности производства, такое как асфальтосмесители «КА-160» (ЗАО «Калокшанский агрегатный завод», Владимирская область), НС-100 (ЗАО «Номбус» г. Омск) или асфальтосмесители ведущих зарубежных производителей. Наш многолетний опыт показывает, что существует комплекс мер, который позволяет довести технические возможности асфальтосмесителей ДС-158 до уровня современных и таким образом выжить на рынке дорожных услуг. Модернизацию асфальтобетонного завода, на примере ДС-158, можно разделить на 2 этапа: 1. Первый этап модернизации 1.1.Модернизация питательного узла – четыре бункера-питателя и раздельное складирование инертных материалов позволяют работать на узких фракциях щебёночных материалов, что необходимо при производстве качественных смесей любых марок; 1.2.Газификация асфальтосмесителей стала нормой и в комплексе с установкой рукавного фильтра типа ЦА-256-3.АБЗ (ЗАО «Спейс-мотор» г. С. Петербург) позволяет соответствовать требованиям существующих норм по экологии (при концентрации пыли на входе в систему пылеулавливания смесителя ДС-158 – 40-45 г/м3, концентрация пыли на выходе из системы – 35 мг/м3); 1.3. Точность дозирования компонентов при автоматизации технологии приготовления асфальтобетонных смесей по нашей разработанной системе: · Точность дозирования инертных материалов – 2%; · Точность дозирования минерального порошка – 1%; · Точность дозирования нефтебитума – 1% (весовое дозирование), что полностью соответствует точности дозирования компонентов у зарубежных производителей (точность дозирования согласно ГОСТ 9128-84: минеральная часть – 3%, минеральный порошок, нефтебитум – 1%, в ГОСТ 9128-97 раздел точности дозирования отсутствует). Скорость набора и выгрузки минерального порошка, за счёт оригинальной системы аэрации, позволяет уложиться в цикл при выпуске и литых смесей, в которых содержание минерального порошка может достигать 22%. Система дозирования нефтебитума позволила получить фактическую точность дозирования 0,5% (погрешность составила 250 г на замес), что соответствует методике лабораторных подборов. Важно отметить, что дозирование минерального порошка должно осуществляться в обязательном порядке через отдельную технологическую линию. Частые попытки осуществления дозировки минерального порошка через весовой бункер инертных материалов – ошибка, так как даже на современных смесителях точность дозирования инертных материалов ниже требуемой для минерального порошка (2% для инертных материалов и 1% для минерального порошка). 2. Второй этап модернизации 2.1. Следует отметить проблему, с которой сталкивается любой эксплуатационник – отсутствие узких фракций щебёночных материалов (отставание рынка от растущих потребностей производственников), что неизбежно приводит при производстве смесей к нехватке или переполнению секций промежуточного бункера и как следствие - к сбою в работе асфальтосмесителя. Эта проблема комплексная, так как связана и с недостаточным количеством кубовидных щебней узких фракций, и с несовершенством конструкции асфальтосмесителя – ёмкость промежуточного бункера крайне мала и не позволяет из-за отсутствия указателей уровня в промежуточном бункере и дистанционной регулировки питателей загрузочных бункеров оперативно корректировать количество материалов в секциях промежуточного бункера. 2.2.Для обеспечения устойчивой работы асфальсмесителя в автоматическом режиме при приготовлении асфальтобетонной смеси, особого внимания требует предварительное дозирование инертных материалов, возможность оперативного дистанционного вмешательства – корректировки дозируемых материалов. Загрузочные бункера-питатели должны иметь дистанционную регулировку, что позволяет оператору оперативно обеспечивать необходимое кол-во материалов в промежуточном бункере. 2.3. Достаточное кол-во песчаных и щебёночных компонентов смеси после отгрохотки – главенствующий фактор: · Целесообразно увеличить промежуточный бункер. Эта модернизация не является очень сложной и при грамотном шефмонтаже может быть выполнена собственными силами; · В промежуточном бункере инертных материалов, после грохота, должно быть условно среднее кол-во материалов, обеспечивающее бесперебойную работу смесителя в автоматическом режиме. Для достижения этого, промежуточный бункер должен иметь указатели уровня инертных материалов по всем секциям. Комплекс перечисленных мероприятий позволяет продлить срок службы асфальтосмесителей ДС-158 и соответствовать растущим требованиям к качеству асфальтобетонных смесей. Ниже приведена общая схема интеграции автоматики ГК «Стромизмеритель» при модернизации асфальтобетонного завода. СХЕМА ИНТЕГРАЦИИ АВТОМАТИКИ ВЕСОВОГО И ОБЪЁМНОГО ДОЗИРОВАНИЯ В АСФАЛЬТНО БЕТОННЫЕ ЗАВОДЫ. Автоматика объёмного дозирования материалов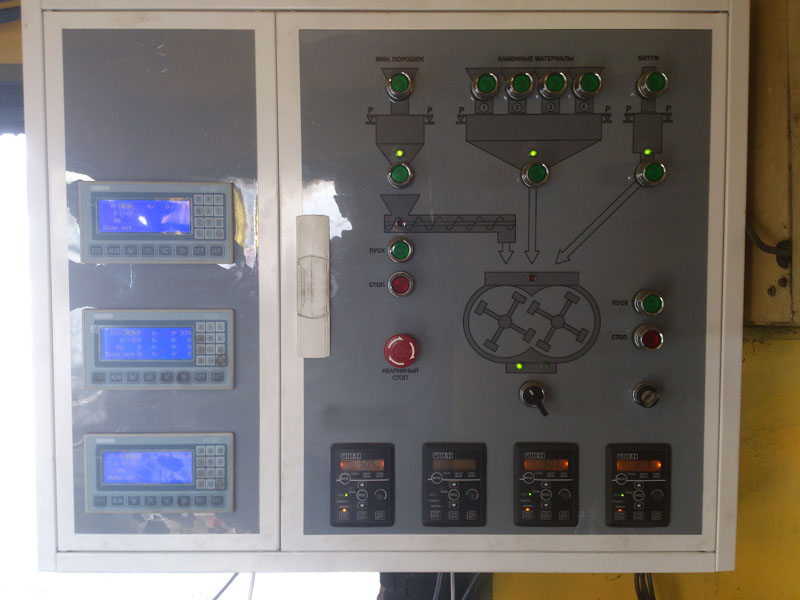 Работу асфальтосмесителя рассмотрим на примере выпуска асфальтобетонной смеси Б-1. Рецепт на асфальтобетонную смесь Б-1 согласно лабораторного подбора: № п.п. | Наименование материала | Кол-во в % | Расход на замес(0,5т) в кг | Точность дозирования компонентов, % | 1. | Щебень гранитный М1200, 5-20 | 30 | 139,5 | 2 | 2. | Отсев гранитный 0-5 | 39 | 181,4 | 2 | 3. | Щебень гранитный М-1200, 5-10 | 15 | 69,8 | 2 | 5. | Отсев доломитовый | 10 | 46,5 | 2 | 6. | Мин. порошок | 6 | 27,5 | 1 | 7. | Н/битум | 7,5 | 37,5 | 1 |
При работе с питателями оснащёнными приводами с частотным регулированием, заслонки на питателях открыты полностью. После розжига сушильного барабана и прогрева системы пылеулавливания, начинается подача инертных материалов в количестве 30% производительности, согласно вышеприведённого рецепта. По мере увеличения температуры материалов на выходе из сушильного барабана, производительность питателей пропорционально увеличивается (рекомендуемый шаг увеличения – 5%) при условно постоянном режиме работы горелки сушильного барабана. По мере накопления материала в промежуточном бункере (после отгрохотки) по данным указателей уровней в секциях, производится анализ с последующей возможной корректурой работы питателей по отдельным компонентам. В данном случае, когда в составе щебня фракции 5-20 мм не достаточное количество фракции 5-10 мм, может потребоваться оперативное вмешательство в работу питателей в процессе отладки выпуска смеси. Система программирования позволяет вводить временные корректировки технологического процесса приготовления смеси, что и делается под руководством инженеров-лаборантов. ПРИНЦИП РАБОТЫ СИСТЕМЫ ПРИГОТОВЛЕНИЯ АСФАЛЬТОБЕТОННОЙ СМЕСИ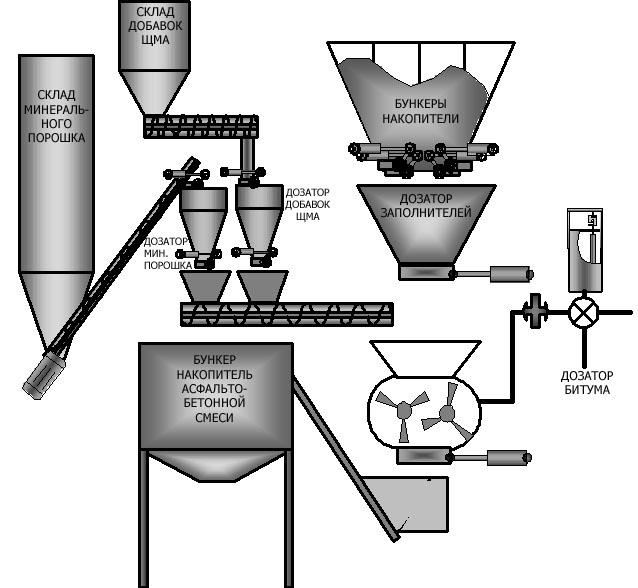 Модернизации подвергается вся весовая система, электрическая часть исполнительных механизмов, исключается максимальное количество конечных выключателей. Дополнительно устанавливаются дозирующие ёмкости для минерального порошка и стабилизирующих добавок для производства ЩМА. Измерение веса в системе происходит с помощью весоизмерительных тензорезисторных датчиков (датчиков силы), затем обрабатывается сигнал, происходит сравнение с тем, что вам необходимо получить, и подаются сигналы на исполнительные механизмы по гибкому алгоритму (под индивидуальные задачи). 1.ДОЗАТОР БИТУМА Максимальную точность взвешивания + 0,1 кг (по опыту нашей работы с 1992 г.) можно достичь при применении узла «Архимеда» 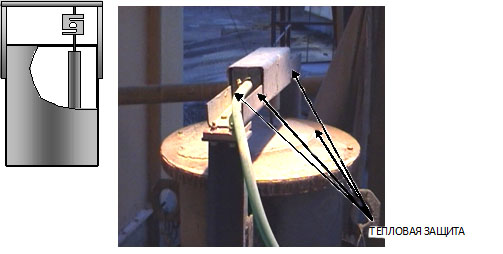 Ёмкость не переставляется и не вывешивается, битумопроводы и система подачи битума в асфальтосмеситель не меняется, что очень важно. При этом ничто не влияет на точность, даже изношенный битумный насос (лишь бы качал). 2.ДОЗАТОР МИНЕРАЛЬНОГО ПОРОШКА Дозирующая ёмкость при её отсутствии изготавливается на нашем предприятии вместе с шлюзовым питателем (при отсутствии шнека) и вывешивается на 3 датчика силы. Рычаги весовых систем не используются и демонтируются. Возможно использование датчиков любого производителя - HBM,CAS,ZEMIC,Тензо М, СКАЛЕС. Точность взвешивания +/-100 гр.
3. ДОЗАТОР ЗАПОЛНИТЕЛЕЙ Дозирующая ёмкость (существующая) так же вывешивается на 4 датчика силы. Рычаги весовых систем не используются и демонтируются. Точность взвешивания (+ 1,0 кг) 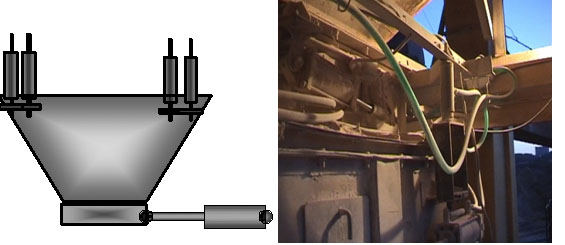
4.НА ОСНОВАНИИ ДАННЫХ О ВЕСЕ СИСТЕМА УПРАВЛЯЕТ: · Магнитным пускателем шнека (питателя) подачи минерального порошка; · Электропневмоклапаном дозирования минерального порошка; · Электропневмоклапаном подачи минерального порошка в горизонтальный шнек или в мешалку асфальтосмесителя; · Электропневмоклапанами дозирования заполнителей 4 ед. по фракциям (промежуточный бункер); · Электропневмоклапаном подачи заполнителей в асфальтосмеситель; · Электропневмоклапаном трёхходового крана дозирования битума; · Магнитным пускателем битумного насоса подачи битума в мешалку асфальтосмесителя; · Электропневмоклапаном разгрузки мешалки асфальтосмесителя; · Магнитными пускателями скипового подъёмника бункера-накопителя готовой смеси (при наличии). |