Особенности использования дробилок различной конструкции в линиях рециклинга стеклобоя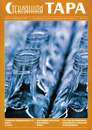 Дробилки являются одними из основных технологических агрегатов, от эффективности работы которых во многом зависит качество переработанного стеклобоя, производимого на линиях рециклинга этого ценного вторичного сырья. При этом эффективность дробления, под которой понимается возможность получения требуемой гранулометрии стекла при заданной производительности процесса измельчения, зависит не только от конструкции и технических характеристик дробильного оборудования, но и от вида исходного материала (стеклотара, листовое стекло, сортовая посуда и пр.) и общих компоновочных решений систем подготовки стеклобоя. Это в первую очередь касается линий переработки привозного стеклобоя, размещаемых на небольших производственных площадях, на которых после операций ручной сортировки предварительно очищенный от камней, пластика и других посторонних предметов стеклобой подается либо в скрубер для последующей мойки его водой, либо в сушильный барабан, если производится сухая» схема очистки. Поскольку при компактном расположении оборудования транспортирование и подъем загрязненного стеклобоя к моечным и сушильным аппаратам чаще всего возможны лишь с помощью элеваторов, имеющих определенные эксплуатационные ограничения по фракционному составу загружаемых мелкокусковых материалов, крупный стеклобой (например, бутылки из-под игристых вин) необходимо сначала измельчать до частиц размером 30-50 мм. Наилучший результат от подобного измельчения достигается при первичном дроблении стеклобоя в щековых дробилках, использование которых не только позволяет эффективно раздавливать толстое стекло в процессе комбинированного (сжатие со сдвигом) движения щек, но и минимизирует появление на выходе нежелательной мелкой крошки и стеклянной пыли, активно образующихся при аналогичном дроблении стекла в молотковых дробилках. Поэтому применение молотковых дробилок для первичного измельчения стекла перед мойкой стеклобоя ограничено из-за быстрого засорения и остекловывания трубопроводов шламовой канализации, а установка их перед подачей обрабатываемого материала в сушильные барабаны нецелесообразна из-за повышенного износа аспирационных патрубков и фильтровального оборудования горячими дымовыми газами, насыщенными большим количеством абразивных частиц стекла.
Чаще всего молотковые дробилки используются в системах переработки и дозирования собственного стеклобоя, возвращаемого в технологию с холодного и горячего концов линий производства стеклянной тары. Причем совместное транспортирование к дробилке влажного стеклобоя после гранулятора и сухого стеклобоя с инспекционного участка контроля качества выпускаемой продукции позволяет существенно снизить уровень пыления при дроблении стекла и усредняет общую влажность полученного материала. Однако совместное дробление сухого и влажного стеклобоя сокращает общий ресурс работы дробилки, поэтому объем подачи в нее смеси стеклобоя из целых бутылок и их осколков разного размера с влажным и измельченным стеклом из гранулятора желательно ограничивать. Такое ограничение достигается либо отдельным дроблением сухого стеклобоя (эта схема используется часто, но имеет недостатки, связанные с пылением), либо с помощью предварительной сортировки стекла по фракциям, которая осуществляется на лотковом вибрационном питателе с классифицирующей решеткой [1]. При использовании питателя данной конструкции уменьшается нагрузка на работу дробильного оборудования, так как во время движения по лотку мелкая фракция стеклобоя просыпается через классифицирующую решетку на конвейер измельченных отходов стекла и минует молотковую дробилку, на домол в которую подаются лишь крупные фрагменты стекла. Также ресурс работы увеличивается, если питатель с классифицирующей решеткой устанавливается под промежуточным накопительным бункером, в процессе заполнения которого стеклом дробилка может находиться в выключенном состоянии. Но установка демпферной емкости со стеклобоем перед дробилкой не всегда возможна и в большинстве случаев, чаще связанных с реконструкцией производства, ограничивается высотой подмашинного помещения цеха выработки стеклотары. Важное значение для улучшения эксплуатационных свойств и обеспечения паспортной производительности дробилок имеют и проектно-технологические решения линий возвратного стеклобоя. Например, неоптимальная компоновка транспортирующего и дробильного оборудования, при которой направление подачи перерабатываемого материала не является перпендикулярным относительно оси ротора дробилки, а загрузка стеклобоя осуществляется не по всей ширине ее загрузочного окна, приводит к неравномерному износу элементов конструкции устройства и более частым ремонтно-профилактическим работам. Если общекомпоновочные решения машинованного цеха предусматривают раздельное измельчение сухого и влажного стеклобоя, то для минимизации пыления дробилки сухого стеклобоя должны работать в условиях пониженного давления или по возможности устанавливаться в изолированных объемах, не связанных с общим воздушным пространством помещения, где кроме оборудования по переработке возвратного стеклобоя могут находиться и вентиляторы обдува печи и стеклоформирующих машин. В ЗАО «Стромизмеритель» при проектировании линий рециклинга стеклобоя учитываются эти факторы и большое внимание уделяется конструктивным особенностям изготавливаемого на своем производстве дробильного оборудования различного функционального назначения. Производимая в ЗАО «Стромизмеритель» дробилка молотковая ДМС-40А предназначена для утилизации отходов при производстве стеклотары, медицинского и листового стекла толщиной не более 12 мм, а также для измельчения неразрушенных капель стекломассы, поступающих на дробление из гранулятора. Данная дробилка (рис. 1) представляет собой устройство непрерывного действия, рабочим органом которой является ротор с шарнирно подвешенными молотками, а основные конструктивные элементы включают в себя корпус, привод, отбойную плиту, регулировочные домкраты и подшипниковые узлы. Корпус дробилки состоит из нижней стационарной части, соединенной с несущей рамой, и двух верхних крышек, которые крепятся на петлях и могут быть разведены для обеспечения легкого доступа к рабочему органу. В верхней части корпуса, изнутри футерованного листами с абразивостойкой наплавкой, шарнирно закреплена отбойная плита из марганцовистой стали, которая с помощью двух домкратов позволяет регулировать рабочий зазор между молотками и плитой, изменяя тем самым размер получаемой после дробления фракции стеклобоя. Технические характеристики дробилки ДМС-40А представлены в табл. 1.
В отличие от молотковых дробилок, ресурс которых при дроблении тарного и листового стекла относительно невысок, двухвалковые дробилки определенной конструкции меньше пылят и имеют меньшую степень износа и истирания рабочих органов, что обусловлено низкой скоростью вращения дробящих элементов [2]. А в связи с тем, что измельченный материал на двухвалковой дробилке разрушается за счет сдавливания при затягивании его между барабанами, а не за счет интенсивных ударных воздействий от вращающихся молотков, получаемая фракция стекла на выходе содержит значительно меньшее количество мелких и пылевидных частиц. 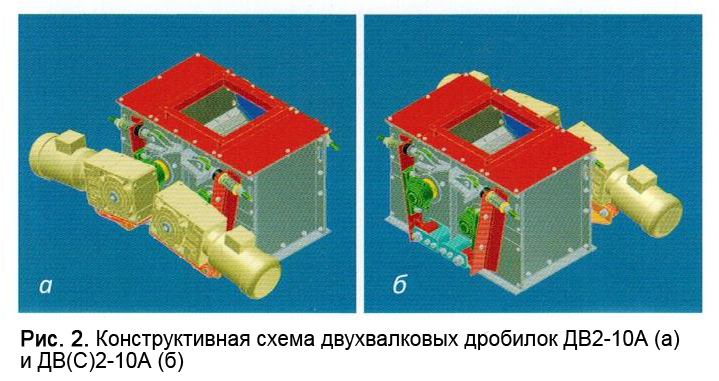 Изготавливаемые в ЗАО «Стромизмеритель» четыре модификации двухвалковых дробилок (ДВ2-10А, ДВ(С)2-10А, ДВ2-15А и ДВ(С)2-15А) выполнены по единой конструктивной схеме (рис. 2) и отличаются друг от друга производительностью и исполнением ребристых барабанов (рис. 3), на цилиндрических поверхностях которых находятся полосы из износостойкого материала разной длины и ширины. Конструктивной особенностью двухвалковых дробилок этих моделей является использование в них «плавающих» подпружиненных валов рабочих барабанов, снабженных в качестве приводов индивидуальными мотор-редукторами. Подпружиненные валы, закрепленные на специальных кронштейнах, имеющих возможность совершать качающееся движение и раздвигаться, предохраняют механизмы дробилки от поломки при попадании в зону работы барабанов вместе со стеклом недробимых тел.
Опытные испытания двухвалковой дробилки при дроблении на ней такого стеклобоя, имеющего в своем составе недробимые материалы и стекло с разной толщиной и разными прочностными характеристиками, выявили как положительные, так и отрицательные моменты, связанные с изменением межосевого расстояния между барабанами при их раздвижке. К положительным свойствам можно отнести эффективное измельчение и отделение различных пробок и пластиковых дозаторов от толстостенных бутылочных горлышек, а к отрицательным - то, что при увеличении межосевого расстояния при попадании труднодробимого предмета в образовавшийся зазор между барабанами может провалиться нераздробленное стекло. Частично этот недостаток устраняется изменением длины и толщины пластин, образующих ребристую поверхность барабанов и формирующих ступенчатый зазор между ними, который предотвращает свободное прохождение осколков листового стекла при незначительной раздвижке рабочих органов дробилки, что особенно важно при переработке привозного стеклобоя разной величины. Основные технические характеристики этих дробилок указаны в табл. 2.
Наряду с молотковыми и двухвалковыми дробилками широкое применение в линиях переработки привозного и собственного стеклобоя находят и роторные дробилки, различные модификации которых для дробления преимущественно листового стекла также изготавливаются в ЗАО «Стромизмеритель» (рис. 4). Роторные дробилки эффективно используются для первичного дробления отходов раскроя и брака при производстве флоат-стекла (несколько таких дробилок производства ЗАО «Стромизмеритель» внедрено на Борском и Красногвардейском стекольных заводах), а также для утилизации закаленного автомобильного стекла (также используется на Борском стекольном заводе) и утилизации строительного и автомобильного стекла триплекс [3]. 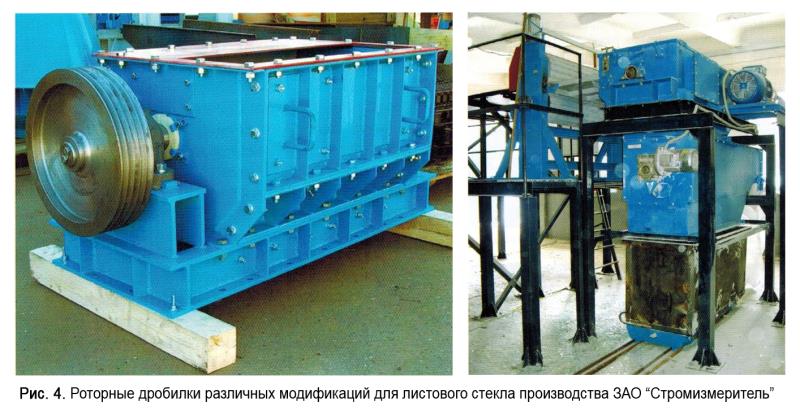
Установка для утилизации стекла триплекс, разработанная в ЗАО «Стромизмеритель», защищена патентом на полезную модель и отмечена в 2011 г. в качестве лауреата Нижегородского конкурса объектов интеллектуальной собственности с присуждением ей диплома 1-й степени и серебряной медали им. И.П. Кулибина.
Другая модификация роторной дробилки, поставляемой ЗАО «Стромизмеритель» в качестве дополнительной опции к скребковому гранулятору стекломассы, предназначена для дробления целых бутылок, плавающих на поверхности ванны гранулятора, и устанавливается в его хвостовой части (рис. 5). В заключение можно отметить, что лишь несколько западноевропейских фирм и ЗАО «Стромизмеритель» предлагают широкий спектр услуг по разработке и комплексной поставке оборудования для переработки собственного и привозного стеклобоя. В дополнение к раз-личному дробильному оборудованию и к проектной документации линий рециклинга стекла ЗАО «Стромизмеритель» изготавливает транспортно-технологическое оборудование, классификаторы стеклобоя, тензометрические весовые дозаторы, грануляторы стекломассы и многое другое. В. В. Ефременков, к. т. н., первый заместитель директора, ЗАО «Стромизмеритель»
Литература 1. Ефременков В.В., Ручкин В.В. Вибрационные транспортно-технологические механизмы для производства стекольной шихты. - Glass Russia. - 2009. - № 6. - С. 24-28.
2. Йене Розенталь. Подготовка возвратного и привозного стеклобоя. - Стеклянная тара. - 2008. - № 4. - С. 4-8.
3. Ефременков В.В., Матвеев А.А. Разработка и изготовление оборудования для вторичной переработки стекла. - Glass Russia. - 2010. -№9.-С.30-37.
|