Разработка технологии изготовления стеклогранулята для производства пеностеклаПеностекло обладает уникальным комплексом физико-химических свойств и по совокупности технических характеристик является наиболее эффективным и перспективным теплоизоляционным материалом, однако его использование и производство в России и республиках бывшего Советского Союза до сих пор остается крайне ограниченным. При этом рост объемов выпускаемой продукции и ввод в эксплуатацию новых производственных мощностей сдерживается не отсутствием современных технологий и соответствующего оборудования, а все еще более высокой удельной стоимостью пеностекла по сравнению с другими композиционными материалами, применяемыми в строительной индустрии. Также при организации рентабельного производства пеностекла возникает ряд проблем, которые во многом обусловлены недостаточным количеством дешевого и в то же время качественного стеклобоя, что связано не только со значительным потреблением собственных отходов стекла непосредственно на предприятиях стекольной промышленности, но и с неразвитой системой централизованного сбора стеклобоя и с отсутствием в большинстве регионов предприятий по его переработке и утилизации. Немаловажное значение при изготовлении пеностеклянных плит, блоков, гравия, а также гранулированного пеностекла имеет и химическая однородность стеклобоя, поступающего с баз вторичного сырья. Подобные отходы разнородного стеклобоя хотя и являются относительно дешевым сырьем (если не принимать во внимание затраты на сбор, сортировку, мойку, сушку, дробление, магнитную и оптическую сепарацию и классификацию), но при их использовании трудно гарантировать постоянство химического состава и стабильное качество пеностекла, особенно выпускаемого на механизированных и автоматизированных линиях с высокой производительностью [1]. Поэтому при больших объемах производства для повышения качества пеностекла целесообразно в качестве исходного сырья использовать специально синтезированное стекло, сваренное в ванных печах из шихты, приготовленной на основе дешевых и недефицитных компонентов, к которым можно отнести отсевы гранитного щебня [2], маршалит, опоку, цеолит и другие природные материалы опал-кристобалитовой группы [3]. Из них особый интерес для стекольной промышленности представляет диатомит - рыхлая или слабосцементированная осадочная порода, образованная в юрский период морскими и озерными отложениями панцирей древних ископаемых водорослей (диатомей). имеющих нанопористую структуру и состоящих более чем на 80 % из аморфного кремнезема, пригодного для применения в качестве полного или частичного заменителя дефицитного кварцевого песка при производстве стеклянной фритты, пеностекла и других видов стекол [4]. В ЗАО «Стромизмеритель» для группы компаний DIAMIX, в состав которой входят научно-технический центр, диатомовый комбинат и крупнейшее в Европе Инзенское месторождение диатомита в Ульяновской области, разработан технологический проект завода, предусматривающий использование этого сырьевого материала для изготовления стеклогранулята, являющегося промежуточным продуктом в производстве высококачественного пеностекла по порошковой технологии. В соответствии с проектом строительство и пуск завода по производству 100 т стеклогранулята в сутки должны осуществляться в одну очередь на свободных площадях диатомового комбината, расположенного в непосредственной близости от карьера по добыче диатомита. Согласно архитектурно-строительным и технологическим решениям основные производственные подразделения и участки завода скомпонованы на небольшой территории размером 52x102 м (рис. 1) и включают в себя: приемное отделение /; транспортную галерею 2 диатомита; участок обработки 3 диатомита; дозировочно-смесительную линию 4; цех выработки 5 стеклогранулята; дымовую трубу б; транспортную галерею 7 и силосный склад готовой продукции 8.
В соответствии с технологией диатомит влажностью 37 - 50 % с карьера, удаленного от диатомового комбината на расстояние не более 1 км, поставляется автомобильным транспортом в приемное отделение завода, где ссыпается в бункер 1 (рис. 2), оснащенный одновальным глинорыхлителем 2, предназначенным для дробления крупной фракции материала.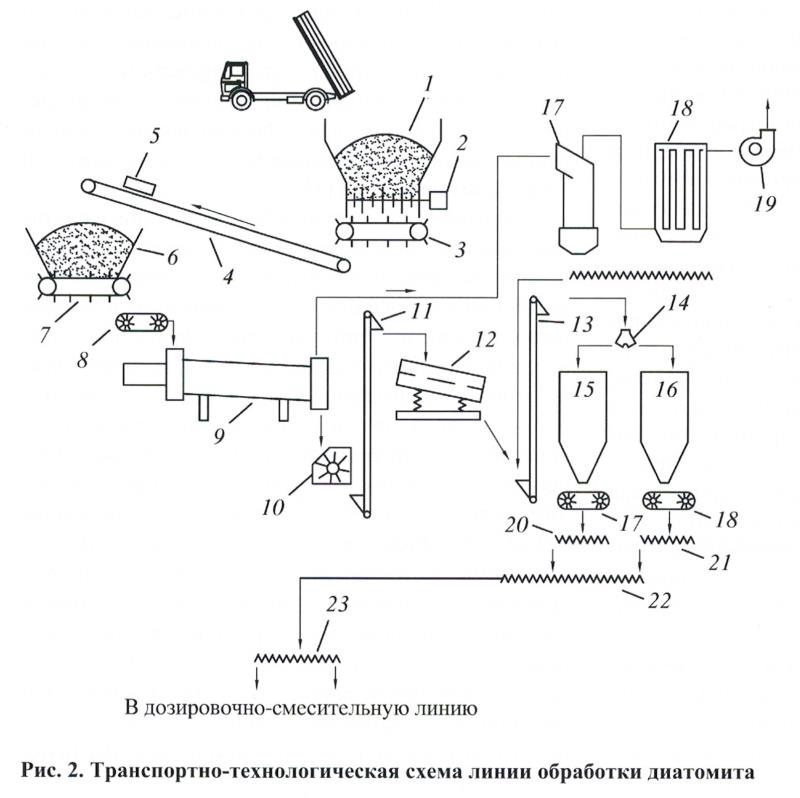 Далее предварительно измельченный диатомит пластинчатым питателем 3 перегружается на галерейный ленточный конвейер 4, оборудованный подвесным магнитным сепаратором 5 для удаления ферромагнитных включений, и транспортируется в промежуточный бункер 6, расположенный на участке обработки диатомита. Поскольку влажный диатомит при транспортировании и промежуточном хранении склонен к комкованию и образованию устойчивых конгломератов различной формы, выгрузка его из бункера 6 и повторная дезинтеграция комьев также производятся пластинчатым питателем 7 и двухвальным рыхлителем 8, установленными перед подачей обрабатываемого материала в прямоточный сушильный барабан 9. Высушенный до конечной влажности 5 % диатомит ссыпается из барабана в молотковую дробилку 10, где окончательно измельчается до частиц размером менее 1 мм, и с помощью элеватора 11 подается на вибрационное сито 12 для фракционирования, в результате которого фракция более 1 мм возвращается на домол, а рабочая фракция посредством элеватора 13 и рукавного переключателя 14 направляется в один из двух накопительных бункеров 15, 16. В эти же бункеры может загружаться и мелкодисперсная пыль из аспирационной системы, состоящей из группы циклонов 17, рукавного фильтра 18 и дымососа 19, создающего разрежение в сушильном барабане. По мере накопления обработанный диатомит выгружается из бункеров 15, 16 с помощью двухвальных рыхлителей 17, 18 и системой винтовых питателей 20, 21 и винтовых конвейеров 22, 23 перераспределяется в надвесовые расходные бункеры 1, 2 (рис. 3) дозировочносмесительной линии, содержащей еще три бункера 3, 4, 5 для загрузки в них соды, доломита и сульфата. В отличие от диатомита эти кондиционные и не требующие дополнительной обработки материалы поступают на завод в мягких разовых контейнерах, разгрузка которых выполняется с помощью кран-балки 6 и станций растаривания биг-бэгов 7, 8, 9. 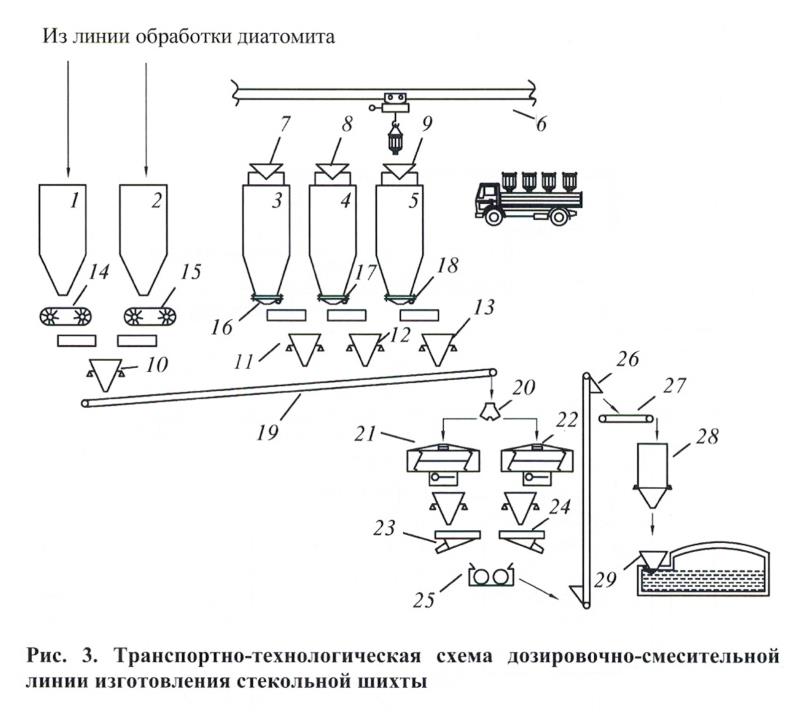 Последующая подача материалов в тензометрические весовые дозаторы 10, 11, 12, 13 производится соответствующими винтовыми питателями загрузки, установленными под двухвальными рыхлителями 14, 15 и вибрационными днищами 16, 17, 18, активизирующими и стабилизирующими истечение компонентов шихты из расходных бункеров. После набора заданных доз все взвешенные материалы разгружаются на сборочный конвейер 19 и через переключатель потока 20 ссыпаются в один из смесителей 21, 22, где они увлажняются и перемешиваются до однородной смеси. Выгрузка готовой шихты осуществляется вибрационными питателями 23, 24, подающими смесь диатомита, соды, доломита и сульфата в двухвалковый пресс 25. Скомпактированная шихта транспортируется элеватором 26 и конвейером 27 в цех выработки стеклогранулята и выгружается в бункер 28, из которого она подается в плунжерно-поворотный загрузчик 29, установленный на загрузочном кармане регенеративной стекловаренной печи с подковообразным направлением пламени и производительностью до 100 т стекломассы в сутки. Операция компактирования не только увеличивает насыпную массу легкой шихты, приготовленной на основе диатомита, но и повышает ее химическую активность, а также снижает пыление и унос легких фракций при загрузке шихты в стекловаренную печь. Из стекловаренной печи 1 (рис. 4) стекломасса по выработочному каналу 2 непрерывной струей сливается на водоохлаждаемый лоток 3, с которого она попадает на гранулятор 4, представляющий собой двухуровневый скребковый конвейер, помещенный в ванну с водой (возможно использование и барабанных грануляторов). От резкого перепада температур, вызванного контактом с водой, стекломасса интенсивно охлаждается и рассыпается на мелкие гранулы, имеющие размер не более 5-8 мм. Увлажненный стеклогранулят с остатками капельной влаги из гранулятора перегружается на ленточный конвейер 5 и поднимается элеватором 6 на более высокую отметку для загрузки материала в трехступенчатый теплообменный аппарат 7 с наклонными жалюзийными решетками (разработка Уральского федерального института имени первого Президента России Б. Н. Ельцина). Данная установка работает следующим образом. Двигаясь вниз под действием силы тяжести по жалюзийным решеткам, разреженный слой материала интенсивно продувается восходящим потоком дымовых газов, отбираемых из стекловаренной печи (температура сушильного агента на входе в аппарат составляет около 300 °С). Противоточное трехступенчатое движение влажного стеклогранулята и горячих дымовых газов способствует эффективному конвективному теплообмену и существенно (по сравнению с сушкой в сушильном барабане) снижает удельный расход теплоносителя. Отработанный сушильный агент с температурой 115 °С попадает в циклоны 8,где очищается от мелкодисперсной пыли, и далее с помощью дымососа 9 сбрасывается через дымовую трубу в атмосферу. А высушенный материал с нижнего обреза последней решетки через разгрузочное окно поступает на галерейный ленточный конвейер 10 и спомощью элеватора 11, рукавного переключателя 12 и конвейера 13 распределяется по силосным банкам 14, 15, 16 склада готовой продукции. Из банок, имеющих общий объем 450 м3, стеклогранулят отгружают в автомобильный транспорт и контролируют платформенными тензометрическими весами 17. Следует отметить, что производительность завода по изготовлению стеклогранулята, равная 100 т в сутки, выбрана из расчета поставок данной продукции в соседние регионы, где также назрела необходимость строительства предприятий по производству различной продукции из пеностекла. Такой объем стеклогранулята позволяет выпускать на его основе около 180 000 м3 пеностеклянных изделий в год, что для одного региона, конечно, много. Оптимальным можно считать производство для одной области 40 000 - 60 000 м3 пеностекла в год, что соответствует мощности стекловаренной печи 20 - 30 т стекломассы в сутки. А для такой производительности более эффективными являются прямоточные печи, которые предлагается использовать именно для производства стеклобоя [5]. Тем не менее, учитывая острую потребность стекольной промышленности в стеклобое и нехватку качественного стеклобоя для производства высококачественного пеностекла со стабильными физико-химическими характеристиками, разработку данного проекта, который проходит в настоящее время Государственную экспертизу, и последующее строительство завода по производству стеклогранулята можно считать своевременным и весьма актуальным. Наряду с разработкой проектной документации завода по изготовлению стеклогранулята специалисты ЗАО «Стромизмеритель» синтезировали несколько составов шихты на основе диатомита (два состава шихты, способ приготовления шихты и технологическая линия запатентованы), провели пробные лабораторные плавки стекла, а также выполнили некоторые исследования физико-химических свойств полученных образцов пеностекла. Основная направленность исследований была связана с расширением сырьевой базы кремнеземосодержащего сырья и снижением энергетических затрат на технологический процесс изготовления стеклогранулята для производства пеностекла. Так, в ходе сравнительных экспериментов по смешиванию, компактированию и плавлению шихты, приготовленной на основе различных видов кремнеземосодержащего сырья (наличие в дозировочно-смесительной линии двух надвесовых бункеров для этих материалов позволяет варьировать составом), выявлено, что шихта, в которой в качестве кремнеземосодержащего компонента используется кварцевый песок, имеет насыпную плотность 1,3 -1,4 т/м3 , позволяющую эффективно загружать ее в стекловаренную печь с помощью наиболее широко применяемых конструкций загрузчиков шихты. Но эта шихта при требуемой влажности 4,5 - 4,7 % практически не компактируется и без использования дорогостоящих связующих материалов не гранулируется. Шихта, в которой кварцевый песок полностью заменен диатомитом, лучше компактируется и плавится при меньших температурах, но имеет сравнительно низкую насыпную плотность 0,5 - 0,6 т/м , что затрудняет процесс загрузки ее в стекловаренную печь, приводит к активному уносу легких фракций в процессе варки стекла и требует при заданной производительности увеличения объемов смесителей и бункеров запаса шихты. Кроме того, подобная шихта склонна к частым зависаниям и образованиям сводов при ее промежуточном хранении. Поэтому авторы предложили и исследовали следующий состав шихты для изготовления стеклогранулята, включающий (массовое содержание): 19 - 23 % кальцинированной соды, 13 - 16 % доломита, 0,45 - 1,0 % сульфата натрия, 30 - 35 % кварцевого песка влажностью 0,5 % и размером фракции 0,1 - 0,63 мм и 28 - 33 % диатомита влажностью 15 - 30 % и размером фракции менее 0,1 мм. Преимуществом предлагаемого состава шихты является то, что частичная замена кварцевого песка на диатомит, имеющий нанопористую структуру, насыщенную влагой, позволяет исключить процесс увлажнения шихты в смесителе, существенно ускорить процессы передачи теплоты внутрь частиц диатомита и снизить температуру варки стекла. При этом снижение температуры варки является результатом как развитой внутренней поверхности пористых частиц диатомита, так и активной гидратации кремнезема. Наличие внутренней влаги в частицах диатомита при варке стекла приводит к тому, что уже при температуре 50 °С во время активизации реакций гидратации кремнезема образуются золи и гели кремниевых кислот. При температуре 200 °С начинается частичное силикатообразование, а при температуре 750 °С - образование эвтетик и жидкой фазы сплавленных эвтетик, а также появление сложных силикатов. Стеклообразование завершается при температуре 1250 - 1350 °С, что на 100 - 150 °С ниже аналогичных температур тепловых процессов, происходящих в шихте, приготавливаемой с использованием кварцевого песка. Дополнительное повышение энергоэффективности процесса производства стеклогранулята из подобной шихты достигается тем, что в технологии приготовления шихты на основе диатомита возможно исключение процесса сушки диатомита в сушильном барабане. Это обусловлено тем, что даже при 30%-ной влажности из-за высоких адсорбиционных свойств диатомита почти вся влага сконцентрирована внутри диатомей и материал сохраняет хорошую сыпучесть при стабильном угле естественного откоса. Сочетание же в составе кремнеземосодержащего сырья кварцевого песка и диатомита, имеющих разную насыпную плотность и разнородные по размеру частицы, позволяет получить более плотную их упаковку при уплотнении на валковом прессе и повысить насыпную плотность скомпактированной шихты до 1,0 - 1,1 т/м3, что существенно улучшает процессы хранения и транспортирования шихты. Также при разнородных по размеру частицах кремнеземосодержащего сырья снижается требуемое давление прессования и уменьшается энергопотребление соответствующего оборудования. Таким образом, разработка технологии изготовления стеклогранулята из шихты, приготовленной с использованием диатомита, позволяет получить исходное сырье для производства пеностекла со стабильными физико-химическими характеристиками, снизить себестоимость получаемой продукции и повысить энергоэффективность технологии изготовления пеностекла. Канд. техн. наук В.В. ЕФРЕМЕНКОВ, д-р техн. наук В.Е. МАНЕВИЧ, Р.К. СУББОТИН (e-mail: stromizmeritel@rambler.ru) Группа компаний "Стромизмеритель" (Россия, г. Нижний Новгород) СПИСОК ЛИТЕРАТУРЫ 1. Шилл Ф. Пеностекло. М., 1965. 307 с. 2. Бобкова Н.М., Баранцева С.Е., Трусова Е.Е. Пеностекло на основе отходов гранитных отсевов Микашевичского месторождения // Стекло и керамика. 2007. № 2. С. 13-16. Bobkova N.М., Barantseva S.Е., Trusova Е.Е. Production of foam glass with granite siftings from the Mikashevichi deposit // Glass and Ceram. 2007. V. 64. N1-2. P. 47 - 50. 3. Казьмина О.В., Верещагин В.И., Абияка А.Н. и др. Температурные режимы получения гранулята для пеностеклокристаллических материалов в зависимости от состава шихты // Стекло и керамика. 2009. № 5. С. 26 - 29. Kaz'mina О.V., Vereshchagin V. I., Abiyaka А. N. et al. Temperature regimes for obtaining granular material for foamed crystal glass materials as a function of the batch composition /7 Glass and Ceram. 2009. V. 66. № 5 - 6. P. 179 - 182. 4. Маневич В.E., Субботин P.К., Никифоров E.А. и др. Диатомит - кремнеземосодержащий материал для стекольной промышленности // Стекло и керамика. 2012. № 5. С. 34 - 39. 5. Киселев В.Н. Стекловаренная печь для производства стеклобоя // Стеклянная тара. 2008. № 3. С. 10 - 11. |