Совершенствование линий транспортирования стекольной шихты в производстве листового стекла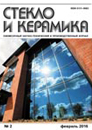 На большинстве действующих заводов по производству листового стекла в России основу поточно-транспортных линий стекольной шихты составляют ленточные конвейеры, транспортирующие по галереям многокомпонентную смесь сырьевых материалов из составного цеха к бункерам загрузчиков стекловаренной печи. Однако на некоторых предприятиях, построенных еще в советский период времени, для транспортирования стекольной шихты используются электровозные тележки, которые в ходе реконструкций и модернизаций постепенно заменяют на конвейерные линии. Замена тележек, управляемых машинистом (засыпщиком шихты), на ленточные конвейеры позволяет при этом не только автоматизировать процесс транспортирования шихты и существенно сократить количество обслуживающего персонала, но и предотвращает возможное возникновение аварийных ситуаций, связанных с эксплуатацией электроподвижного транспортного оборудования [1]. В ООО «Стромизмеритель» за последние годы было выполнено несколько проектов, в которых предусматривалась подобная замена морально и физически устаревших электровозных тележек на современные транспортно-технологические линии, состоящие из ленточных конвейеров, весовых дозаторов шихты и стеклобоя, а также реверсивных передвижных конвейеров-челноков. Одним из таких проектов, реализованных нижегородской компанией в 2015 году, является линия дозированной подачи шихты и боя к стекловаренной печи в строящемся производстве листового стекла на Курловском стекольном заводе «Символ» во Владимирской области.
Новое производство на данном заводе (пуск его планируется на конец третьего квартала 2016 года) размещается на месте бывшего цеха листового стекла, выработка которого в течение многих лет осуществлялась по методу вертикального вытягивания (метод Фурко или ВВС). Как и на всех аналогичных предприятиях, транспортирование шихты к стекловаренной печи на заводе «Символ» производилось с помощью электроприводных вагонеток, курсирующих по галерее от промежуточных бункеров запаса шихты в составном цехе до бункеров загрузчиков в машинно-ванном отделении. Соотношение шихта/стеклобой при таком способе загрузки обеспечивалось только с помощью объемного дозирования, в ходе которого на слой из нескольких порций шихты, разгружаемых из вагонеток в бункеры загрузчиков, засыпался более тонкий слой стеклобоя. Очевидно, что подобная послойная загрузка, производимая в ручном режиме управления, не обеспечивала равномерного перемешивания сырьевых материалов и приводила не только к нарушению условий их плавления, но и к термической неоднородности получаемой стекломассы. В ходе проектирования нового производства листового стекла, вырабатываемого вертикально-горизонтальным способом (метод Кольберна или ВГС), в ООО «Стромизмеритель» была разработана и изготовлена полностью автоматизированная линия, в которой заданное соотношение шихта/стеклобой достигается непрерывным весовым дозированием сырьевых материалов, загружаемых в стекловаренную печь. Причем выбор непрерывного способа весового дозирования и соответствующего данному способу оборудования был обусловлен наличием четырех промежуточных бункеров запаса шихты и определенными строительными ограничениями для использования более габаритных дозаторов дискретного действия. Ранее на этом заводе в производстве стеклянной тары уже использовалась система непрерывного весового дозирования шихты и боя, построенная с помощью дозатора непрерывного пропорционального марки ДНП-20К [2]. Дозаторы этой модели отличаются простотой конструкции и содержат: два питателя шихты и стеклобоя; два весоприемных устройства, контактирующих с транспортерной лентой конвейера; датчик движения ленты и блок управления. Наряду с простотой еще одним преимуществом подобных дозаторов является то, что они имеют малые габариты и легко встраиваются в существующие конвейерные системы подачи шихты и стеклобоя. Но есть у них и существенные недостатки, связанные со сложностью тарирования и калибровки весоизмерительной системы дозатора ДНП-20К, систематическим накапливанием ошибок дозирования в его блоке управления, а также с нестабильностью измерений, вызванной вибрациями и колебаниями степени натяжения ленты весового конвейера. Поэтому в новых линиях транспортирования шихты и стеклобоя к стекловаренным печам, находящимся в производствах листового стекла и стеклянной тары, предусмотрены усовершенствованные весовые дозаторы непрерывного действия типа ДВНД-650, которые имеют другой принцип работы и не содержат указанных недостатков. Усовершенствованная конструкция одной из модификаций дозатора ДВНД-650/Ш (Рис.1), предназначенная для непрерывного дозирования шихты, включает в себя: питающий шнек 1 с диаметром винта 250мм и длиной 1500мм; ленточный весовой конвейер 2 с шириной ленты 650мм и межосевым расстоянием 3000мм, шарнирное крепление 3 конвейера на основании 4; тензометрическую весовую подвеску 5, одним концом связанную с неподвижной рамой 6, а другим концом соединенную с консольной частью7 конвейера 2; датчик скорости 8, расположенный на валу приводного барабана конвейера, и устройство управления (не показано). Принцип работы этой модификации дозатора заключается в следующем. Питающий шнек 1 с регулируемой производительностью подает шихту из промежуточного бункера 9 хранения на ленту весового конвейера 2, вращение которой контролируется в устройстве управления с помощью датчика 8 скорости, генерирующего определенное количество импульсов пропорциональное перемещению ленты. Одновременно тензометрическая весовая подвеска 5 воспринимает массу конвейера 2 с дозируемым материалом и передает текущее значение весовой нагрузки в устройство управления для вычисления массы расходуемого материала, прошедшего через дозатор за контролируемый период времени. Если же дозатор используется не для измерения расхода, а для выдачи определенной порции дозируемого материала, то в устройстве управления применяется режим автоматического упреждения, обеспечивающий устранение погрешности, связанной с просыпанием материала после отключения питающего устройства. 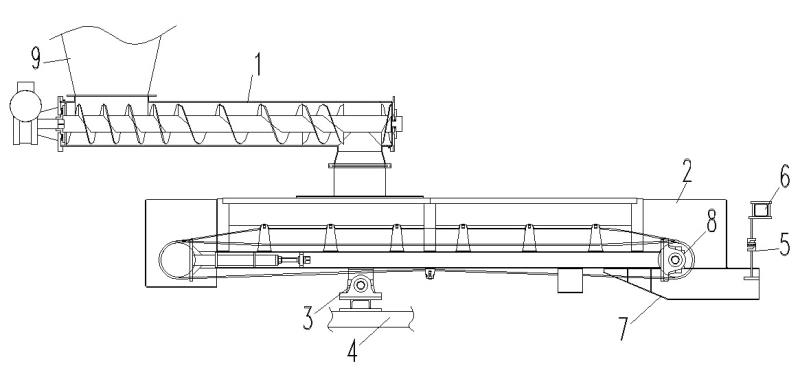
| Рис. 1. Дозатор весовой непрерывного действия со шнековым питающим устройством |
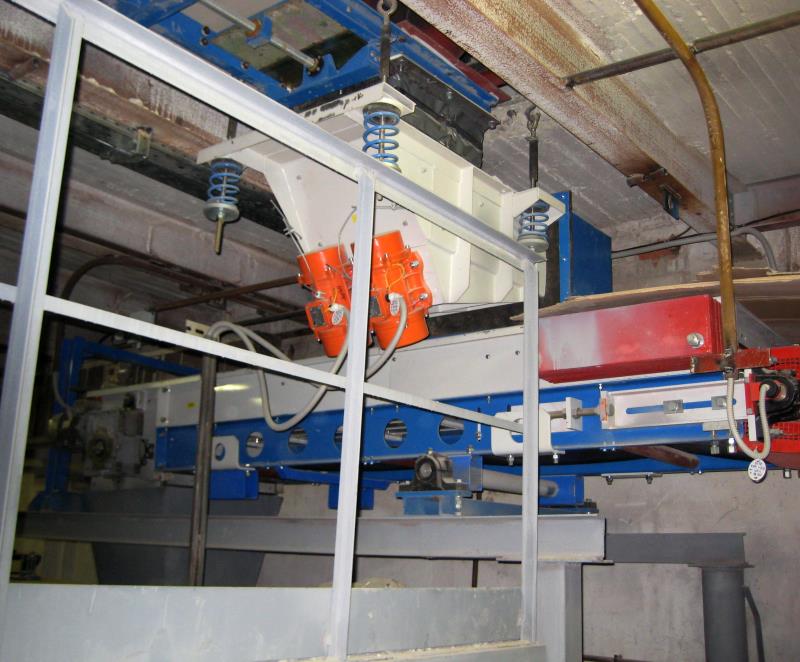
| Рис 2. Дозатор весовой непрерывного действия с вибрационным питающим устройством |
В конструкции другой аналогичной модели дозатора ДВНД-650/ПВ (Рис.2), предназначенной как для дозирования шихты, так и для дозирования стеклобоя, в качестве питающего устройства применяется вибрационный питатель с шириной лотка 500мм и длиной 1200 – 1600мм. При этом обе эти конструкции дозаторов (одна со шнеком, а другая с вибрационным питателем) могут использоваться как совместно, так и раздельно при дозировании различных сырьевых материалов. Совместное использование их в линиях дозированной подачи шихты и стеклобоя целесообразно лишь в тех случаях, когда шихта расходуется не из разгрузочной воронки смесителя, а из промежуточного бункера запаса, имеющего больший объем. Это объясняется тем, что порция шихты, выгружаемая из смесителя непосредственно на один из транспортных механизмов линии, минуя бункер запаса, имеет заданный вес, обусловленный постоянным объемом смешивающего агрегата. Дополнительное непрерывное дозирование шихты в этих условиях не требуется, а величина дискретной порции стеклобоя, подавемого в общую линию транспортирования, определяется исходя из веса выгружаемой из смесителя шихты и заданного соотношения этих материалов. В связи с тем, что в составном цехе стекольного завода «Символ» используется промежуточное хранение шихты, линия дозированной подачи шихты и стеклобоя к бункерам загрузчиков стекловаренной печи нового производства листового стекла содержит обе модификации этих дозаторов, работающих в непрерывной взаимосвязи друг с другом. Шихта в данной линии (Рис.3) выгружается из бункеров 1 запаса с помощью винтовых питателей 2 и далее транспортируется винтовым конвейром 3, ленточным ковшовым элеватором 4 и ленточным конвейером 5 (этот участок линии существующий) к непрерывному весовому дозатору 6 со шнековым питающим устройством 7. Последующее перемещение отдозированной шихты вместе с добавленным к ней в заданном соотношении собственным возвратным стеклобоем производится галерейным и промежуточным конвейерами 8, 9. 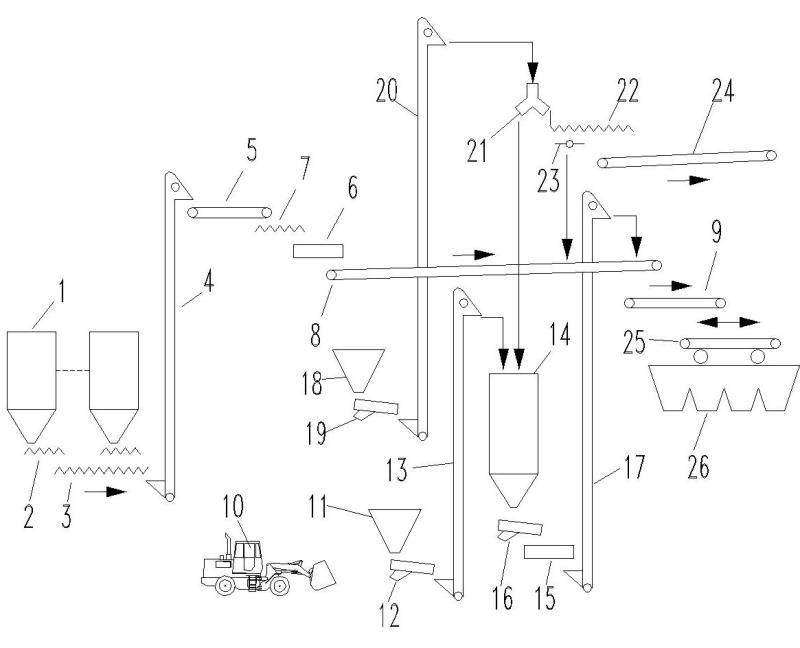 | Рис. 3. Линия дозированной подачи шихты и стеклобоя |
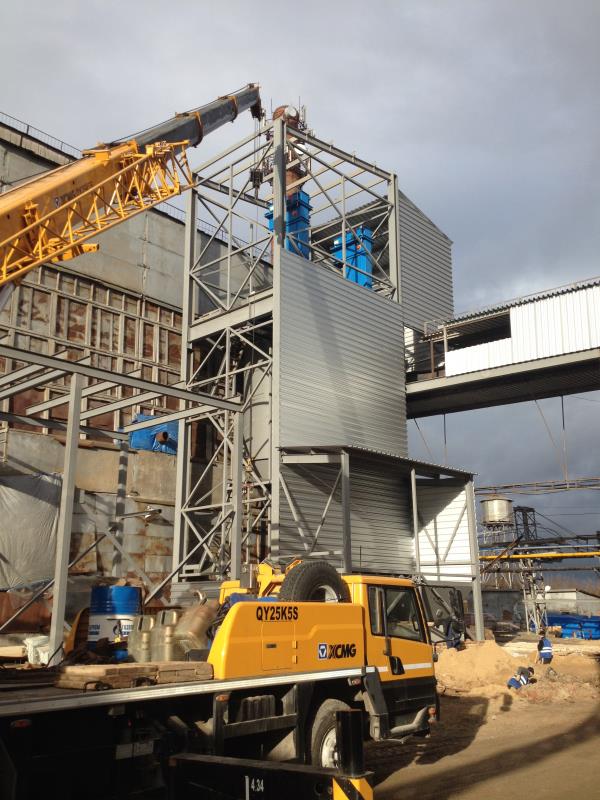 | Рис. 4. Башня дозирования стеклобоя |
Формирование заданного соотношения шихта/стеклобой при этом реализуется во вновь построенной башне стеклобоя (Рис.4), входная подача материала в которую осуществляется с помощью фронтального погрузчика 10 (см. схему Рис. 3). Башня имеет вертикальную компоновку оборудования и состоит из приемного бункера 11 стеклобоя с вибрационным питателем 12 разгрузки, ленточного ковшового элеватора 13, силосной банки 14, непрерывного весового дозатора 15 с вибрационным питающим устройством 16 и ленточного ковшового элеватора 17. Кроме того, в башне стеклобоя предусмотрена резервная подача шихты, осуществляемая по транспортной цепочке «приемный бункер 18 – вибрационный питатель 19 разгрузки – ленточный ковшовый элеватор 20 – переключатель потока 21 – винтовой конвейер 22 – шиберный затвор 23». Винтовой конвейер 22 в процессе резервной загрузки перегружает шихту с указанных транспортных механизмов и подает ее либо на существующий галерейный конвейер 24 стеклотарного производства, либо через шиберный затвор 23 - на галерейный конвейер 8 производства листового стекла. Резервная подача шихты при этом также осуществляется фронтальным погрузчиком, который загружается на специально оборудованном участке составного цеха, расположенном недалеко от башни стеклобоя. Предусмотрена в башне и резервная загрузка стеклобоя в силосную банку 14, которая в случае выхода из строя основной транспортной цепочки, состоящей из вибрационного питателя 12 и элеватора 13, может производиться с помощью элеватора 20 и переключателя потока 21. По окончании процессов взаимосвязанного дозирования шихты в составном цехе и стеклобоя в башне смесь этих материалов, пройдя операцию магнитной сепарации, перегружается с промежуточного конвейера 9 на конвейер-челнок 25, установленный на бункере 26 загрузчиков стекловаренной печи. Конвейер-челнок 25 (еще его часто называют «шаттл») представляет из себя реверсивный ленточный транспортер, установленный на перемещающуюся по рельсовым путям рамную конструкцию с электроприводом. Направление движения шаттла по рельсам зависит от полноты и равномерности заполнения бункера и может в соответствии с алгоритмом управления как совпадать с направлением движения его ленты, загружающей шихту, так и быть противоположным. Полнота же заполнения и равномерность распределения загружаемой смеси шихты и стеклобоя по всей ширине фронта загрузки бункера контролируется соответствующими датчиками верхнего и нижнего уровня, по сигналам с которых система управления формирует команды на движение конвейера-челнока и его ленты в ту или иную сторону относительно продольной оси стекловаренной печи. Так как подобные конвейеры-челноки с реверсивным движением ленты имеют в отличие от других конструкций меньшую длину, равную примерно половине ширины фронта загрузки бункера, они получили наибольшее распространение в линиях загрузки шихты и стеклобоя в регенеративные стекловаренные печи с поперечным направлением пламени. Обычно в таких линиях подача смеси шихты и стеклобоя с галерейного или промежуточного конвейера на шаттл производится по наиболее оптимальному направлению, совпадающему с продольной осью стекловаренной печи (перпендикулярно направлению перемещения шаттла). Оптимальная загрузка конвейера- челнока в этом случае может производиться и двумя самостоятельными линиями, транспортирующими шихту от двух или даже от трех смесителей. Существуют также схемы линий, в которых шаттл загружается как одним, так и двумя промежуточными конвейерами, расположенными параллельно оси перемещения конвейера-челнока. Подобное взаимное расположение транспортирующих механизмов возможно тогда, когда вход транспортной галереи выполнен не с торца машинно-ванного цеха, а с боку и, если есть определенный запас по высоте (не менее 4-5 метров) в пространстве между точкой загрузки конвейера-челнока и нижней строительной отметкой ферм перекрытия печного отделения. Такое ограничение связано с необходимостью установки над шаттлом дополнительного бункера (воронки), объединяющего потоки загружаемой шихты с двух промежуточных конвейеров. В тех же случаях, когда из-за особенностей взаимного расположения составного и машинно-ванного цехов, а также из-за ограничений по высоте печного отделения сложно осуществить оптимальную загрузку шаттла с реверсивным движением ленты, применяются конвейеры-челноки с однонапрвленным вращением ленты. Как правило, загрузка этих конвейеров производится под углом или по оси их перемещения, а сами конвейеры-челноки имеют длину, которая равна примерно ширине фронта засыпки шихты и стеклобоя в бункер загрузчиков стекловаренной печи. Определенным недостатком таких конструкций, кроме их увеличенной в два раза длины, является требование к организации и более длинных технологических и ремонтных зон выкатки шаттлов. Тем не менее, такие конструкции конвейеров-челноков тоже необходимы, и один подобный конвейер с однонаправленным движением ленты внедрен и успешно эксплуатируется на производстве флоат-стекла в г. Красногвардейске Ставропольского края. Другой передвижной конвейер с удлиненным межосевым расстоянием (расстояние между осями приводного и натяжного барабанов составляет около 9 метров) включен в проект реконструкции аналогичного производства Саратовского института стекла, где также планируется замена электровозных тележек шихты. Еще один масштабный проект, связанный с заменой тележек на автоматизированные конвейерные линии, выполнен ООО «Стромизмеритель» в 2015г. для «Эй Джи Си «Борский стекольный завод»». Согласно этому проекту (реализация его уже началась) по транспортной галерее, имеющей длину около 500м, с помощью системы ленточных конвейеров, которые заменят электровозные тележки (Рис. 5 ), будет транспортироваться не увлажненная смесь материалов, а взвешенные в составном цехе сухие сырьевые компоненты стекольной шихты. Взвешенные по новой схеме компоненты далее будут выгружаться на систему, состоящую из нескольких галерейных конвейеров, и в соответствии с общей циклограммой работы оборудования подаваться в новое смесительное отделение, расположенное в непосредственной близости от стекловаренных печей. Смесительное отделение, строительство которого (Рис. 6) находится в завершающей стадии, выполнено по вертикальной схеме и содержит три смесителя немецкой компании ЕIRICH (два рабочих, один резервный). Близкое расположение этих смесителей по отношению к стекловаренным печам двух флоат-линий позволит после реконструкции не только оперативно загружать свежеприготовленную смесь в бункеры загрузчиков, но и исключит ухудшение качества шихты за счет сокращения в 10 раз времени ее транспортирования. 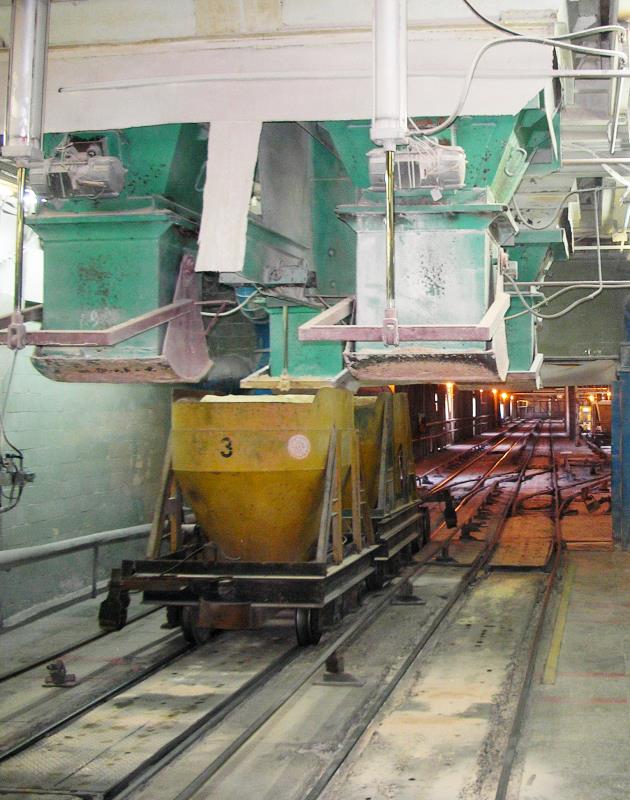
| 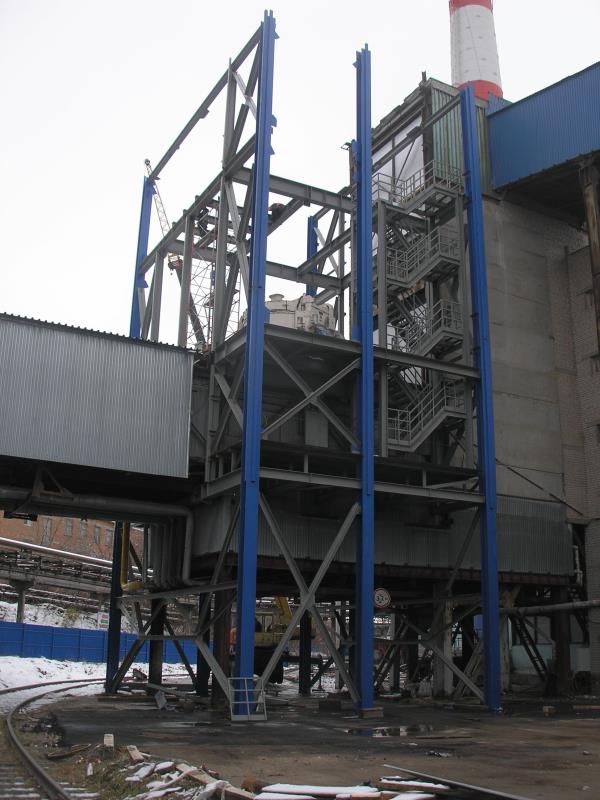
| Рис. 5. Электровозные тележки для транспортирования шихты | Рис. 6. Строительство нового смесительного отделения на Борском стекольном заводе |
Есть и другие реализованные проекты линий транспортирования шихты и стеклобоя, в которых применены аналогичные технические решения с использованием различного транспортно-технологического и дозировочного оборудования производства ООО «Стромизмеритель». В.В. Ефременков, к.т.н., первый заместитель директора ООО «Стромизмеритель» Литература 1. Ефременков В.В. Особенности проектирования линий транспортирования стекольной шихты // Стекло и керамика. 2010. №12. С.3–6. 2. Ефременков В.В., Субботин К.Ю., Хаймович М.М. Система дозированной подачи шихты и боя в стекловаренную печь // Стекло и керамика. 2001. №6, С.3–4. |